The instrumentation and control project consists of several stages: calculation, basic engineering, detailed engineering, pre-installation testing, installation, commissioning, spare parts delivery and after-sales back-up.
The multidisciplinairy project team consists of: a project manager, mechanical engineer, process engineer, planning engineer, quality control engineer, electrical engineer and an I&C engineer. In a later phase the site manager, site engineer and commissioning engineer are added. The team is supported by purchase, cost control and spare-parts personnel.
For different industries the project team formation and project stages may change.
Some team functions may be parttime; mostly planning, purchase and cost control personnel.
Often for electrical and I&C engineering one engineer will be used.
Calculation:
In this stage the I&C engineer supports the precalculation projects engineer with detailed info of suitable solutions for specific measurement and control systems. And he will check necessary client spec’s.
Basic engineering:
In this stage the I&C engineer develops P&ID’s in a multidisciplinairy team , write spec’s for equipment, he will check all client spec’s and he will negotiate with client engineers. He will also attend HAZOP (Hazardous and Operability Analysis) meetings with the multidisciplinairy project team, client engineers and extrnal specialists for defining right safety control functions and explosion proof requirements.
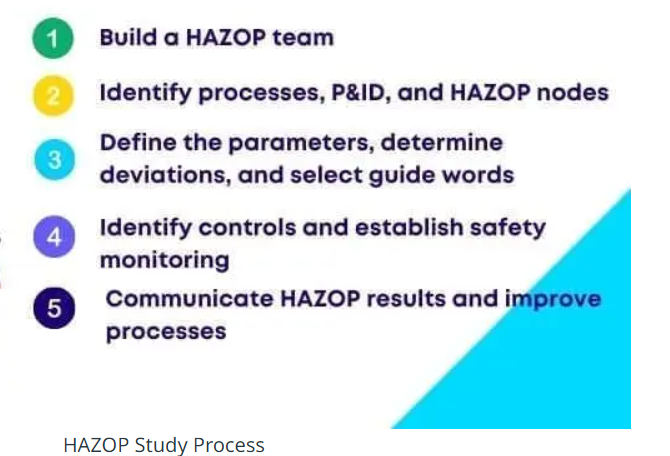
Detailed engineering:
In this stage the I&C engineer will develop, nowadays mostly with enhanced software tools: instruments list, I/O list, alarm and trip settings list and he will write the datasheets of instruments and electrical equipment. Wiring diagrams, panel drawings, terminal and cable lists are also often automatically generated or developed by installation companies; the I&C engineer will initiate and check this. In a multidisciplinairy team the I&C will advise and check proper installation of all material and he will check the purchasing proces. In this stage the I&C engineer will also develop the installation description for selection of installation companies. He will also make automation and control loop documents; see the control page. The I&C engineer will also select the right installation company and automation company; see control page. Finally, he shall make the commissioning and maintenence manuals.
Pre-installation testing:
In this stage the I&C engineer will do the necessary testing of equipment at the vendor factories. He will check the delivery of all documents, like: material certificates (3.1B/C), explosion proof certificates and all manuals. The delivery of commissioning spare parts will be checked. He will also do all checking and testing at the installation company and automation company.
Installation:
The I&C engineer will support the site engineer and site manager with regards to all I&C items. He will support the site engineer with on-site testing and negotiations. He will check right delivery of orderrd equiment and commissioning spare-parts.
Commissioning:
The I&C engineer will support the commissioning engineer with all his requested items. He will also make all documents and manuals as-built.
Spare-parts delivery and after-sales back-up:
The I&C engineer will initiate with PM right delivery of spare-parts, mostly for 3-5 years operation of the installation.
Please find attached a typical description of a complete project:
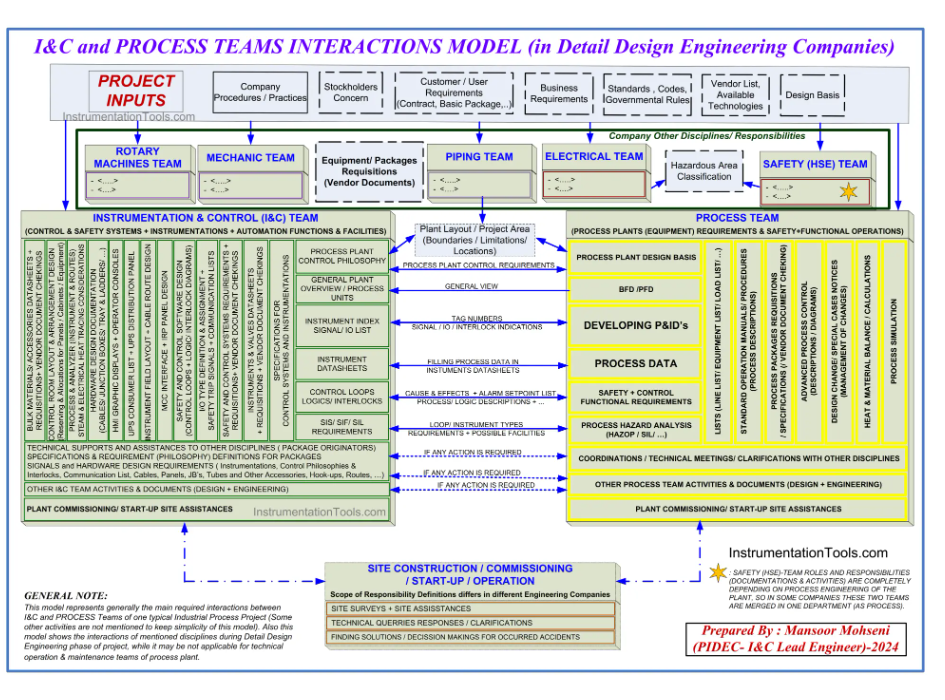